What Is In-Die Tapping for Manufacturing?
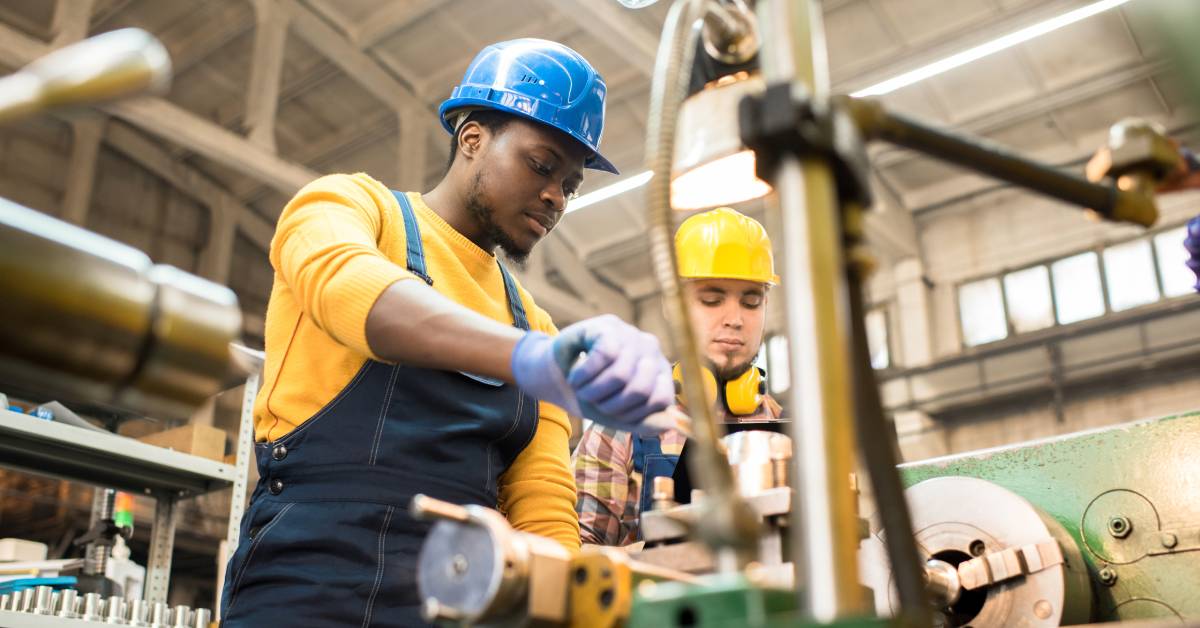
In-die tapping is an innovative manufacturing process that integrates threading capabilities within stamping operations, allowing manufacturers to produce tapped holes directly in the stamping die without requiring a separate tapping machine. This integration speeds up production, reduces the need for secondary processing, and minimizes material handling. By threading during stamping, in-die tapping provides efficiency that traditional methods can’t match, making it an appealing option for industries seeking streamlined production. Read on to learn more about what in-die tapping is for manufacturing.
Benefits of In-Die Tapping
The primary benefit of in-die tapping is improved efficiency. By combining tapping and stamping in one operation, manufacturers eliminate extra steps and reduce labor costs. This process also shortens cycle times, enabling manufacturers to produce more parts within a given timeframe. Additionally, in-die tapping improves precision, as the alignment of taps and dies is controlled within a single machine. This accuracy reduces defects, leading to higher-quality components with fewer errors and scrap materials.
Industries That Use In-Die Tapping
In-die tapping is particularly beneficial for industries that require high-volume production and precise threading, such as automotive, electronics, and appliance manufacturing. Automotive components, for instance, often have tapped holes in structural parts, and in-die tapping offers the accuracy and speed needed to meet production demands. Electronics manufacturers also benefit, as this method allows for the creation of small, accurately tapped holes in delicate parts, enhancing consistency and quality for intricate assemblies.
Challenges in In-Die Tapping
While in-die tapping offers advantages, it also comes with challenges that manufacturers must consider. Tooling wear is a primary concern, as the constant impact from the tapping process can lead to faster deterioration of dies and taps. Additionally, setting up an in-die tapping system requires precise calibration, making it essential to have skilled technicians on hand. Manufacturers often need to weigh these factors when deciding on in-die tapping, as frequent maintenance can offset time-saving benefits if not carefully managed.
Servo or Mechanical In-Die Tapping Systems
When choosing an in-die tapping system, manufacturers can select either servo or mechanical systems based on their specific needs. Servo systems offer precision control over tapping speed and depth, which is ideal for sensitive materials or components requiring exact tolerances. Mechanical systems, on the other hand, are often simpler and more cost-effective, making them suitable for high-volume production where speed is the priority. Determining whether servo or mechanical in-die tapping best fits a production line depends on factors such as material type, part complexity, and desired production output.
Now that you know what in-die tapping is and how it benefits manufacturing, you can see why it’s become an essential process in various industries. Understanding the differences between servo and mechanical in-die tapping systems can help manufacturers make informed choices that align with their production goals and operational needs.