Common Reasons for Heavy Equipment Failure
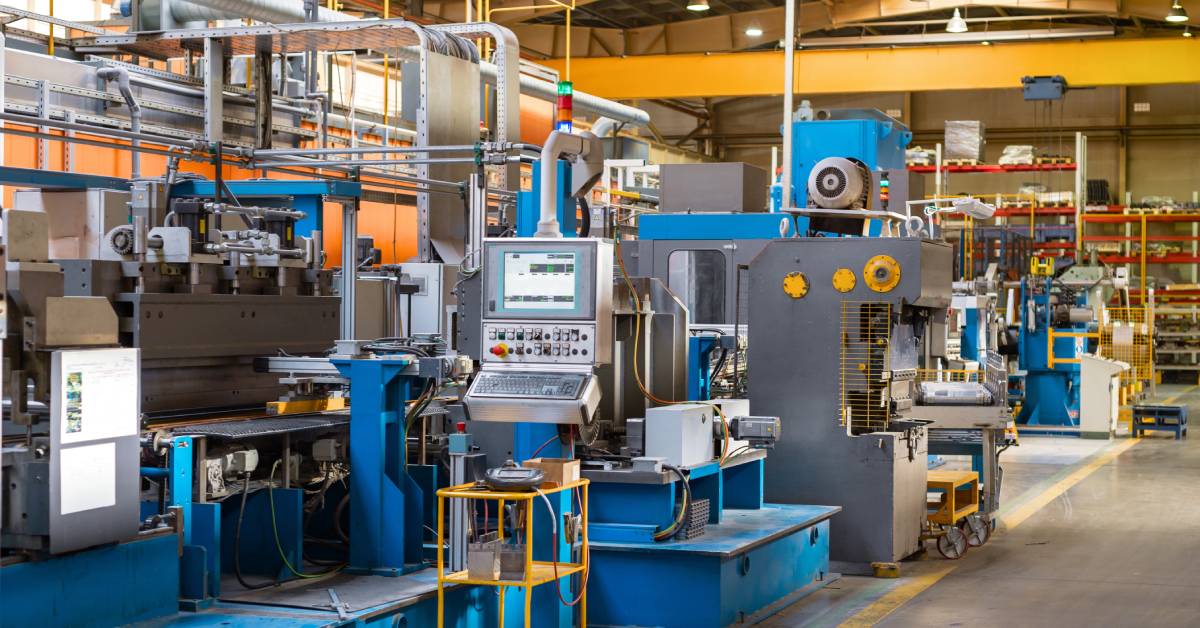
Heavy equipment is the backbone of any construction and industrial project, keeping operations moving smoothly and on schedule. However, even the most advanced machinery is vulnerable to breakdowns.
Why do these failures occur and how can you minimize disruptions? Below, we look at the common reasons or heavy equipment failure and how you can prevent downtimes or delays.
Overheating and Lack of Lubrication
Overheating can cause significant damage to engines, hydraulic systems, and other critical parts. Often, this is a result of inadequate ventilation, clogged filters, or excessive workloads.
Poor lubrication compounds the issue, as friction between mechanical components generates heat, leading to accelerated wear. Regularly checking and replacing lubricants, cleaning filters, and avoiding overburdening your equipment can help you avoid the costly consequences of overheating.
Electrical System Failures
Electrical issues are a frequent cause of downtime, whether due to corroded wiring, failed sensors, or battery malfunctions. Heavy equipment operates in demanding environments where extreme temperatures, dust, and vibrations degrade electrical components over time. Maintenance teams should regularly inspect wiring, clean terminals, and test voltage output to identify minor issues before they lead to costly failures.
Hydraulic System Issues
Many heavy machines rely on hydraulic systems to perform essential tasks, such as lifting, digging, or moving materials. A single leak in a hydraulic line can bring operations to a halt.
Such systems are complex and require precise pressure levels and clean fluids to function effectively. Contamination, worn seals, or insufficient fluid levels are all common culprits behind hydraulic failures. Routine fluid analysis and seal inspections are critical for ensuring peak performance.
Worn Out or Misused Components
Excessive wear and tear often occur when components work beyond their intended capacity or don’t get replaced often enough. Operators play a crucial role here. Misuse of equipment, such as overloading or operating at improper angles, can degrade components faster than expected.
Proper training for operators and adhering to manufacturer guidelines for usage and part replacement avoid unnecessary wear. Always use OEM (Original Equipment Manufacturer) parts for replacements, as they maintain compatibility and durability.
Environmental Factors
Weather, terrain, and other environmental factors significantly impact the longevity of your heavy equipment. For instance, prolonged exposure to moisture can lead to rust and corrosion, while working in areas with fine dust particles can clog filters and damage internal systems.
Adapting to the environment by using equipment covers, specialized filters, or increasing the frequency of maintenance checks ensures the conditions don’t get the better of your machines.
Prolonging the Life of Heavy Equipment
A proactive approach to maintenance is vital to prolong the life of your heavy equipment. Implement a structured maintenance schedule that includes daily inspections, fluid top-offs, and regular part replacements. Ensuring that operators are well-trained and following best practices is another foundational step.
Keep an eye on performance metrics tracked by telematics systems, as these can alert you to potential issues before they escalate. With these habits in place, you will significantly extend your equipment’s life and lower repair costs.
Heavy equipment failures can halt productivity and increase costs exponentially. However, the right approach to maintenance and care can save your operation from these unwanted setbacks. By understanding the common causes of failure and implementing preventative measures, you’ll improve equipment reliability and boost the efficiency of your entire operation.