The Critical Role of Gas Detectors in Workplace Safety
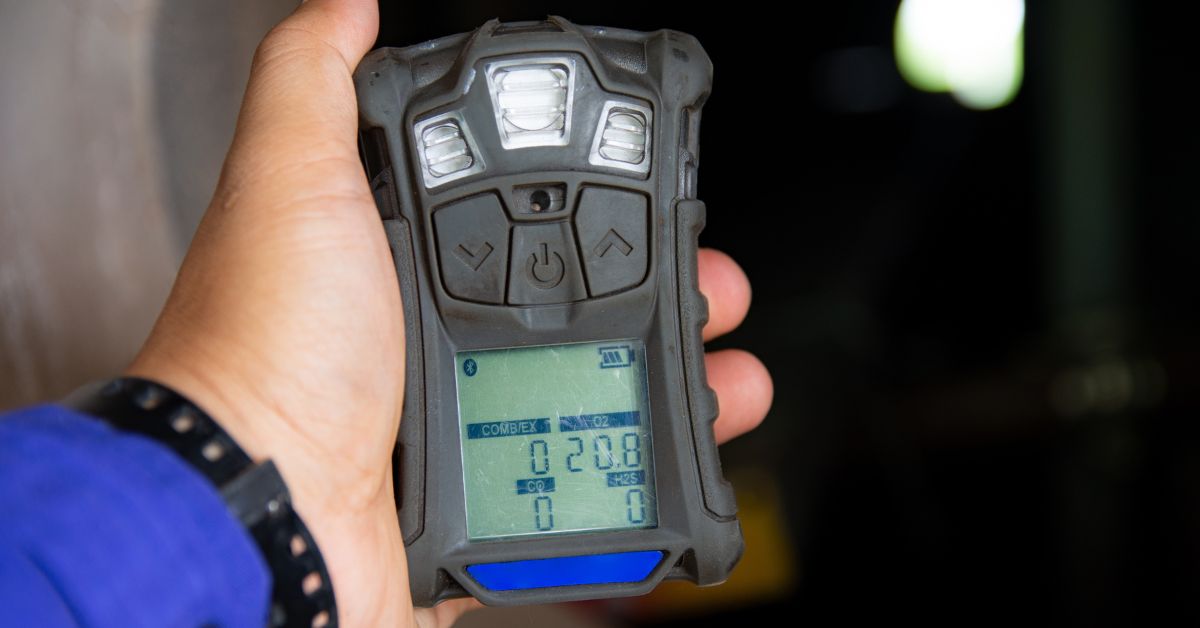
Vigilance is key when it comes to maintaining a safe workplace. For facility managers, safeguarding the well-being of employees against unseen threats is an ongoing challenge. In the realm of occupational safety, gas detectors stand as silent sentinels, offering a critical defense against the insidious presence of hazardous gases. Read on to learn more about the critical role of gas detectors in workplace safety.
Importance of Gas Detectors
Gas detectors serve as the first line of defense, ensuring the air we breathe is safe. With the ability to sense the presence of various gases, these devices can signal alarm at the first whiff of danger. The importance of gas detectors lies in their capability to facilitate.
Early Detection of Hazardous Gases
The presence of hazardous gases can be life-threatening. Gas detectors are the silent watchdogs that detect these gases long before they reach levels that can cause acute or chronic health issues.
Prevention of Accidents and Health Risks
Gas detectors prevent workplace catastrophes by alerting personnel to immediate action. They also detect non-toxic gases that harm the environment and nearby communities.
Compliance With Safety Regulations
Safety regulations require the use of gas detectors, especially in sectors where the risks of gas exposure are high, such as oil and gas, chemical manufacturing, and mining. Compliance with these regulations protects workers and shields organizations from legal and financial liabilities.
Types of Gas Detectors
Understanding the different types of gas detectors is essential for selecting the right tools to meet safety needs.
Single Gas vs. Multi-Gas Detectors
Single gas detectors can detect one type of gas, which is optimal for work environments with known and specific gas hazards. Multi-gas detectors, on the other hand, can monitor several gases simultaneously, making them adaptable to more complex industrial settings.
Different Detection Technologies
Gas detectors use varied technologies to function. These can include:
- Catalytic bead sensors are best for detecting combustible gases.
- Infrared sensors are ideal for sensing certain hydrocarbons.
- Electrochemical sensors are precise in detecting toxic gases like carbon monoxide and hydrogen sulfide.
- Photoionization detectors (PIDs) are effective for gauging volatile organic compounds (VOCs).
Understanding these technologies can help when selecting the ideal gas detector for your specific application.
Best Practices for Gas Detector Use
Simply having gas detectors on-site is insufficient. Their effectiveness hinges on proper implementation and regular oversight.
Proper Placement and Maintenance
You need to place gas detectors strategically to provide the earliest possible warning. Regular maintenance, including battery checks and sensor cleanings, is paramount to ensure accurate readings.
Training for Staff
A well-informed workforce is the backbone of any safety protocol. Providing comprehensive training on gas detector operation and response procedures can significantly improve safety outcomes.
Regular Calibration and Testing
You must calibrate gas detectors at regular intervals to maintain precision. Routine testing under various conditions ensures that detectors are operational and ready to provide timely warnings.
Gas detectors play a critical role in workplace safety, and understanding how they work is essential for industrial workers. Stay safe and ensure your workplace has the necessary gas detection technology to protect your most valuable asset—your people.